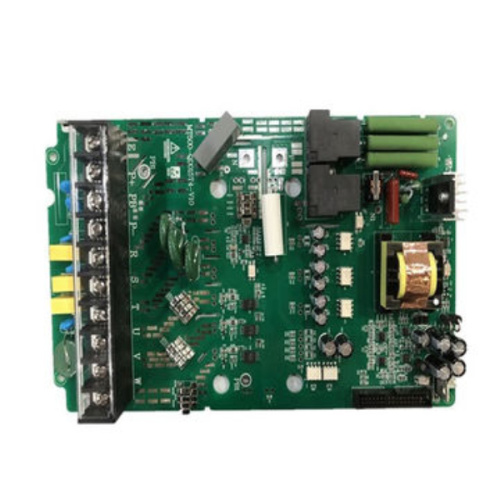
PCB Assembly Contract Manufacturing Service
-
$0.50≥1 Piece/Pieces
- Min. Order:
- 1 Piece/Pieces
- Min. Order:
- 1 Piece/Pieces
Your message must be between 20 to 2000 characters
Contact NowWhat is the difference between wave soldering and reflow soldering?
Wave soldering and reflow soldering are two common soldering methods of Turkey PCB Assembly electronic products in the PCBA Manufacturing production process. This article mainly introduces the difference between wave soldering and reflow soldering. First, it introduces the respective characteristics of Wave Solder for PCBA and PCBA reflow soldering. Working principle, secondly, the difference between wave soldering and reflow soldering is analyzed from two aspects.
Introduction to wave soldering
Wave soldering refers to the melting of solder (lead-tin alloy) through an electric pump or electromagnetic pump sprayed into the solder wave peaks required by the design, and it can also be formed by injecting nitrogen into the solder pool, so that the electronic components are pre-installed The printed board realizes the soft soldering of the mechanical and electrical connections between the solder ends or pins of the Electronic Components and the printed board pads through the solder wave.
Wave soldering process: insert the component into the corresponding Electronic Components hole → pre-apply flux → preheating (temperature 90-100℃, length 1-1.2m) → wave soldering (220-240℃) cooling → remove excess plug-in feet → Inspection of.
The surface of the wave surface is covered by a layer of oxide skin, which remains almost static along the entire length of the solder wave. During the wave soldering process, the PCB touches the front surface of the tin wave, the oxide skin is broken, and the tin wave in front of the PCBA The pleats are pushed forward, which means that the entire oxide skin and PCB are moving at the same speed as the solder joints of the wave soldering machine: when PCBA enters the front end (A) of the wave surface, the substrate and pins are heated, and before leaving the wave surface ( B) Before, the entire PCB was immersed in the solder, that is, it was bridged by the solder, but at the moment it left the end of the wave, a small amount of solder adhered to the pad due to the wetting force, and due to surface tension, There will be a state of small shrinkage centered on the lead. At this time, the wetting force between the solder and the pad is greater than the cohesion of the solder between the two pads. Therefore, a full and round solder joint will be formed, and the excess solder leaving the wave tail will fall back into the tin pot due to gravity.
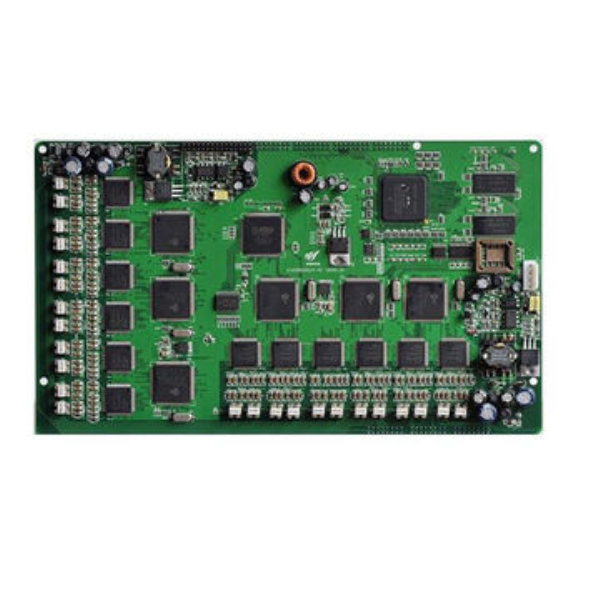
Reflow soldering technology is not unfamiliar in the field of electronic manufacturing. The components on the various boards used in our computers are soldered to the circuit board through this process. There is a heating circuit inside this equipment to heat air or nitrogen. After heating to a high enough temperature, blow it to the circuit board where the component has been attached, so that the solder on both sides of the component will melt and be bonded to the motherboard. The advantage of this process is that the temperature is easy to control, oxidation can be avoided during the welding process, and the manufacturing cost is easier to control.
Reflow soldering principle
Due to the continuous miniaturization of electronic product PCB boards, chip components have appeared, and traditional soldering methods can no longer meet the needs. In Mixed Assembly, reflow soldering is used, and most of the components soldered by PCB assembly are chip capacitors, chip inductors, mount transistors and diodes. With the development of the entire SMT technology becoming more and more perfect, and the emergence of a variety of chip components (SMC) and mount devices (SMD), Surface-Mount (SMT) & BGA Assembly as the reflow soldering process technology and equipment of the mounting technology part have also been corresponding With the development of, its application is becoming more and more extensive, and it has been applied in almost all electronic product domains.
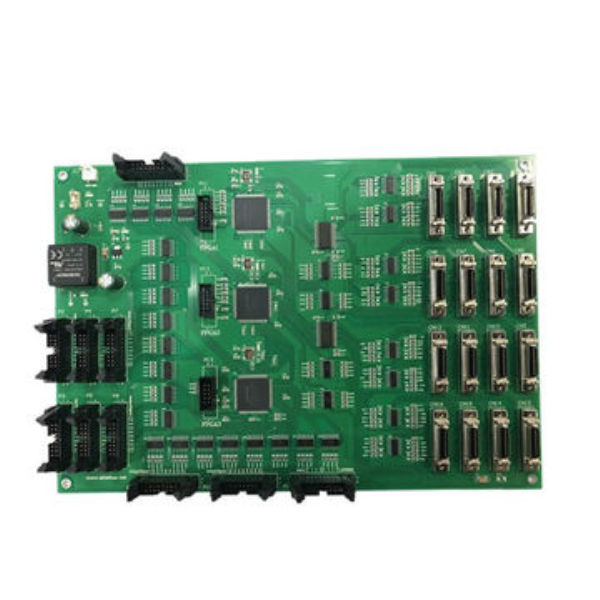
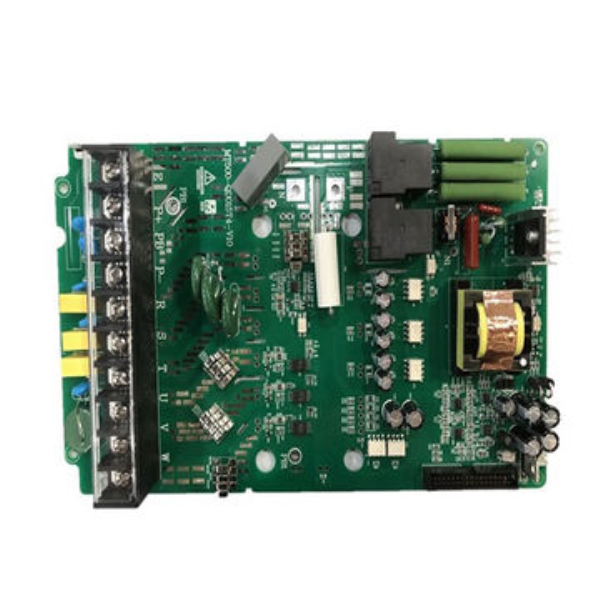
One difference:
The reflow soldering process is to remelt the solder paste pre-distributed on the printed board pads to realize the mechanical and electrical connection between the solder ends of the surface mount components or the pins and the printed board pads.
Wave soldering has a new soldering process with people’s awareness of environmental protection. In the past, tin-lead alloy was used, but lead is a heavy metal that can cause great harm to the human body. So now there is the production of lead technology. It uses *tin-silver-copper alloy* and special fluxes, and the soldering temperature requires higher and higher preheating temperature. It is also necessary to set up a cooling zone workstation after the PCB board passes through the soldering zone. This is to prevent thermal shock. On the other hand, if there is ICT, it will affect the detection.
Wave soldering can basically be interpreted as: it is different from reflow soldering for soldering of slightly larger and smaller components. However, reflow soldering heats the board and components, which is actually to liquefy the solder paste that was originally brushed on. , In order to achieve the purpose of connecting the components with the board.
1. Reflow soldering passes through the preheating zone, reflowing zone and cooling zone. In addition, wave soldering is suitable for manual boards and dispensing boards, and all components are required to be heat-resistant. The surface of the wave must not have components that used to be SMT solder paste. SMT solder paste boards can only be reflow soldered, not Use wave soldering.
2. Wave soldering is to melt the tin bar into a liquid through a tin bath, and use the motor to stir to form a wave, so that the PCB and the parts are welded together. It is generally used for the soldering of the hand plug-in and the smt glue board. Reflow soldering is mainly used in the SMT industry. It uses hot air or other heat radiation to melt the solder paste printed on the PCB and solder the parts.
3. The process is different: wave soldering must first spray flux, and then go through preheating, soldering, and cooling zones.
Two different points:
Wave soldering is mainly used for soldering plug-ins; reflow soldering is mainly used for soldering chip components
1. Wave soldering is to melt the tin bar into a liquid through a tin bath, and use the motor to agitate to form a wave, so that the PCB and the parts are welded together. It is generally used for the soldering of hand plug-ins and the glue board of SMT. Reflow soldering is mainly used in the SMT industry. It uses hot air or other heat radiation to melt the solder paste printed on the PCB and solder the parts.
2. The process is different: wave soldering must first spray flux, and then go through preheating, soldering, and cooling zones. The reflow soldering passes through the preheating zone, reflowing zone, and cooling zone. In addition, wave soldering is suitable for manual boards and dispensing boards, and all components are required to be heat-resistant. The surface of the wave must not have components that used to be SMT solder paste. SMT solder paste boards can only be reflow soldered. Wave soldering.
Related Keywords