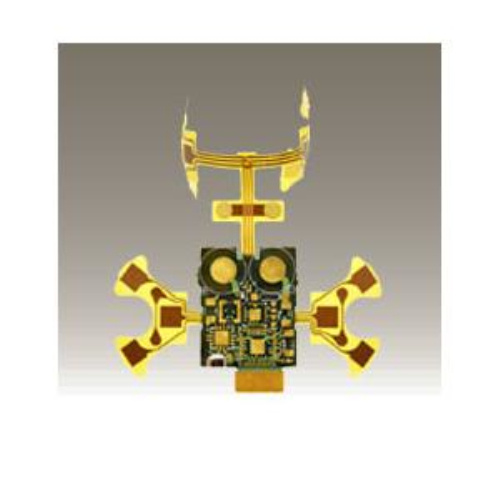
High Quality Stiffener Material Rigid-Flex PCB
-
$0.02≥1 Piece/Pieces
- Min. Order:
- 1 Piece/Pieces
- Min. Order:
- 1 Piece/Pieces
Your message must be between 20 to 2000 characters
Contact NowHow do you make a rigid flex PCB?
The main steps involved in the rigid-flex custom pcb fabrication process are as follows:
1. High Quality PCB Products Flex: applies adhesive/coating on the copper layer-the first and most important step in rigid-flex PCB manufacturing is to apply a suitable adhesive on the thin copper layer (in the ring Choose between oxygen or acrylic adhesive).
2. Add copper foil-use lamination or electroless plating to add a thin layer of copper foil on the adhesive.
3. Drilling-mechanically drill ultra-small to medium to large-sized holes into the flexible substrate.
4. Plating through holes-this is a key step in rigid-flex PCB manufacturing, because it requires special care and precision.
5. Coated anti-corrosion coating-After through-hole electroplating, a photosensitive anti-corrosion coating is applied on the flexible surface. LPI (liquid imageable image) is very suitable for this purpose. It can be applied by roll coating, spray coating or curtain coating.
6. Etching and peeling-After etching the copper film, chemically peel the resist from the circuit board.
7. Coverlay Layers-The cover layer used as a solder mask is applied on the top and bottom of the flexible circuit to provide absolute protection for the PCB.
8. Cut the flexible line-this step involves cutting the flexible line, also known as blanking. Processes such as hydraulic punches and dies are used for cutting flexibility.
9. Laminating-After the blanking process, the flexible circuit is laminated between the rigid parts.
Then conduct electrical tests on the laminated flexible circuit to ensure its High Quality PCB Products Flex.
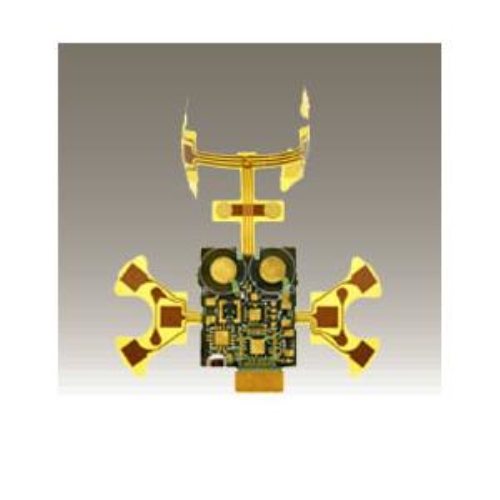
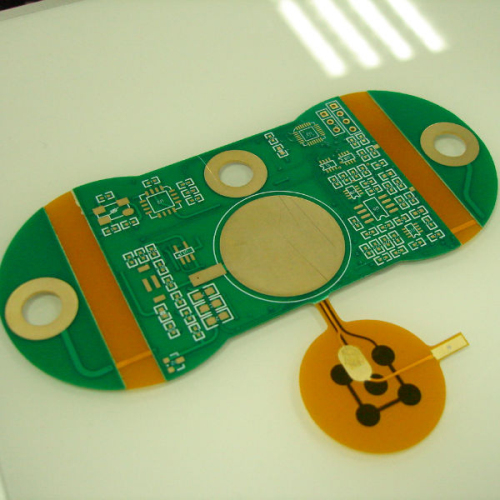
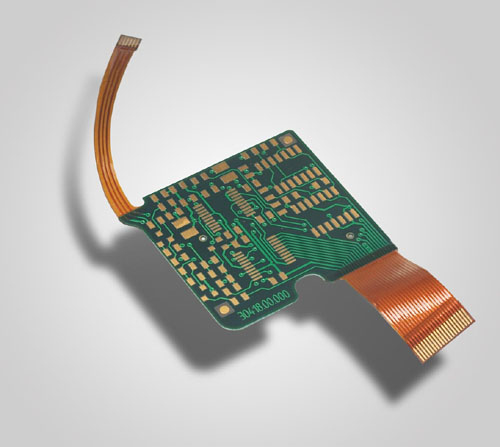
Related Keywords