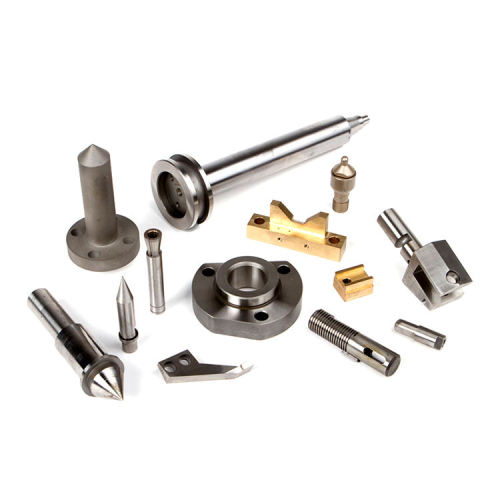
CNC milling metal parts
-
$5.00≥10 Piece/Pieces
- Min. Order:
- 10 Piece/Pieces
- Min. Order:
- 10 Piece/Pieces
- Transportation:
- Ocean, Land, Express, Air
- Port:
- Guangdong, Shenzhen
Your message must be between 20 to 2000 characters
Contact NowPlace of Origin: | shenzhen |
---|---|
Productivity: | 1000 |
Supply Ability: | 1000 |
Payment Type: | T/T,Paypal |
Incoterm: | CFR,FOB,CIF,EXW,FCA,DDP,DDU,Express Delivery |
Certificate: | ISO9001 |
HS Code: | Non |
Transportation: | Ocean,Land,Express,Air |
Port: | Guangdong,Shenzhen |
The precision parts processing industry has very strict standards, and there are different processes such as cutting in and cutting out. The size will also have different specific requirements according to the product, and the machining accuracy requirements will be different. Generally speaking, the precision of precision machining is very high, and sometimes it can even be accurate to the micron difference below 1mm. If the size difference is large, the product becomes scrap and needs to be reworked to meet the requirements, a time-consuming and laborious process. Sometimes all the raw materials will be scrapped, resulting in an increase in cost. At the same time, the parts are inevitably unusable, so there are many requirements for precision parts processing.
So what are the requirements for precision parts processing?
(1) Usually, due to the cutting amount of parts, heating and cutting force for parts rough and precision are different, in order to ensure the machining accuracy of parts, so we must respectively carry out the processing of rough parts and precision mechanical parts. If rough machining and precision machining continue, precision machining parts will be lost because of the difference in stress.
(2) Rationality of equipment selection. The processing of rough parts does not require high processing accuracy, but mainly to reduce the processing allowance, so precision processing needs very high precision machine tools. In the process of precision parts, the heat treatment process is often arranged. The position of the heat treatment process is arranged as follows: in order to improve the cutting performance of the metal, such as annealing, normalizing, tempering, etc., it is generally arranged before the machining of the mechanical parts.
(3) Generally speaking, almost all precision parts are processed with a heat treatment process, which can improve the cutting performance of the metal. Precision parts processing and manufacturing not only need the accuracy and stability of machine tools and tools, fixture accuracy to ensure, but also need precision measuring instruments for calibration and measurement. Some are in the process of processing, and some are after inspection.
A fire two masses of hot forging and warm forging parts finishing process is to change the appearance of the raw materials directly to a specific product or different products, the process of the technological process, this process is called machining process is also a benchmark, precision parts processing process is more complex, precision parts processing technology standard can be divided into according to the craft of casting, forging, stamping, welding, Heat treatment, processing, assembly, and other categories. Precision parts processing often refers to the floorboard of the whole process of CNC machining parts and machine assembly, and other processes such as cleaning, inspection, maintenance, oil seal, and turning method change the surface properties of raw materials or semi-product, this process is called numerical control processing, the corresponding central tool path difference form of switch, Precision parts systems are equipped with linear and circular interpolation.
product description
Material
|
1) Aluminum: AL 6061-T6, 6063, 7075-T etc.
|
2) Stainless steel: 303,304,316L, 17-4(SUS630) etc.
|
|
3) Steel: 4140, Q235, Q345B,20#,45# etc.
|
|
4) Titanium: TA1,TA2/GR2, TA4/GR5, TC4, TC18 etc.
|
|
5) Brass: C36000 (HPb62), C37700 (HPb59), C26800 (H68), C22000(H90) etc.
|
|
6) Copper, bronze, Magnesium alloy, Delrin, POM,Acrylic, PC, etc.
|
|
Finish
|
Sandblasting, Anodize color, Blackenning, Zinc/Nickl Plating, Polish.
|
Power coating, Passivation PVD, Titanium Plating, Electrogalvanizing.
|
|
Electroplating chromium, electrophoresis, QPQ(Quench-Polish-Quench).
|
|
Electro Polishing,Chrome Plating, Knurl, Laser etch Logo, etc.
|
|
Main Equipment
|
CNC Machining center(Milling), CNC Lathe, Grinding machine.
|
Cylindrical grinder machine, Drilling machine, Laser Cutting Machine,etc.
|
|
Drawing format
|
STEP,STP,GIS,CAD,PDF,DWG,DXF etc or samples.
|
Tolerance
|
+/-0.01mm ~ +/-0.05mm
|
Surface roughness
|
Ra 0.1~3.2
|
Inspection
|
Complete inspection lab with Micrometer, Optical Comparator, Caliper Vernier,CMM.
|
Depth Caliper Vernier, Universal Protractor, Clock Gauge, Internal Centigrade Gauge.
|
|
Capacity
|
CNC turning work range: φ0.5mm-φ150mm*300mm.
|
CNC milling work range: 510mm*1020mm*500mm.
|
Picture case
Related Keywords