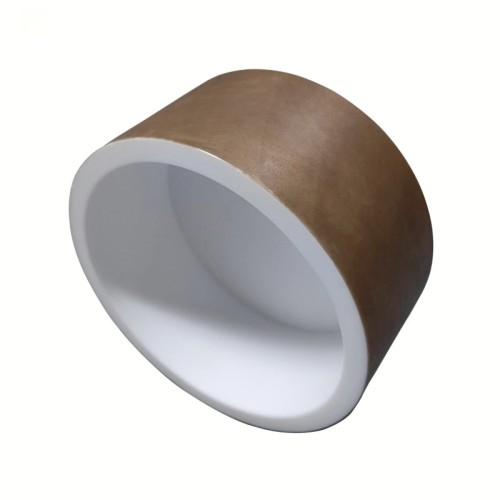
PTFE Etching CNC Machining Service Custom Machining Parts
- Min. Order:
- 1
- Min. Order:
- 1
- Transportation:
- Ocean, Land, Air, Express
- Port:
- Shenzhen, Guangzhou, Hongkong
Quantity:
Your message must be between 20 to 2000 characters
Contact NowBasic Info
Basic Info
Supply Ability: | 1000 |
---|---|
Transportation: | Ocean,Land,Air,Express |
Port: | Shenzhen,Guangzhou,Hongkong |
Product Description
Product Description
Polytetrafluoroethylene lining general equipment/Polytetrafluoroethylene lining equipment/Polytetrafluoroethylene (Poly tetra fluoroethylene, abbreviated as PTFE), commonly known as the “king of plastics”, is a tetrafluoroethylene as a monomer polymerization of polymers. It is white waxy, semi-transparent, with excellent heat and cold resistance, and can be used for a long time at -180-260C. This material is characterized by resistance to acids, alkalis, and various organic solvents, and is virtually insoluble in all solvents. At the same time, PTFE is characterized by high temperature resistance, and its coefficient of friction is extremely low, so it can be used for lubrication, and it has also become an ideal coating for the inner layer of easy-to-clean water pipes.
PTFE lining can be divided into two types: loose lining and tight lining. Loose lining is generally the PTFE tape winding in the corresponding mold, sintering molding on the mold, demolding sets into the equipment, flanging that is completed; features are equipment steel body and lining PTFE plate gap between the applicable temperature change is not large and for the positive pressure of the pipeline, the reaction cylinder, etc.; the advantages of the process is simple, less investment, molding fast; the disadvantage of a large change in the environment of the negative pressure and temperature is prone to cause the PTFE plate deflated. The disadvantage is that in the environment of negative pressure and temperature change, it is easy to cause deflation, bubbling, flange edge cracking and other problems; in the electric spark detection, the vacuum on some PTFE plates may not be detected.
We are engaged in the production and sales of fluorine lined pipe fittings, fluorine lined pipes and fluorine lined compensator series products. The products are widely used in petroleum, chemical, metallurgy, pharmaceutical, electric power and other industries.
PTFE lining molding technology
PTFE lining molding technology will use PTFE lining, metal mesh, fluoroplastic fusion membrane (polyperfluoroethylene propylene FEP or polytetrafluoroethylene-perfluoropropyl vinyl ether copolymer PFA), fiberglass, adhesive and metal shell. Diamond grid metal mesh of PTFE anti-corrosion products to overcome and improve the square grid metal mesh (or other forms) the technical problems that exist in PTFE lining three-dimensional rotational molding technology is a high-fluidity engineering plastics in a substitute lining mold, heating the workpiece, and at the same time make the mold rotate around the rotary axis and rotating axis, so that the inner surface of the inner cavity of the workpiece is coated with a layer of uniform, seamless molten engineering plastics. The sealing performance, corrosion resistance and service life of fluorine lined valves are greatly improved.
PTFE lining molding technology includes pre-molding process and sintering molding process.
1, PTFE lining molding technology in the pre-molding process using elastic mold molding, workpiece cavity lining parts of the inner and outer walls under equal pressure difference, the elastic mold to make full use of its elasticity so that the cavity has been loaded with PTFE powder compression and tightly adheres to the lining wall, and PTFE lining thickness to maintain a consistent, a complete solution to the complex shape of the workpiece cavity of the molding technology and the problem and the thickness of the lining is not consistent, resulting in local stress concentrations caused by the lining of fluorine valves. It completely solves the problems of molding technology for complex shaped workpiece cavities and cracks caused by local stress concentration due to inconsistency of lining thickness. At the same time, to overcome the sintering process curing reaction (exothermic reaction) speed inconsistency leads to local stress concentration and bring the consequences of cracks.
2, PTFE lining molding technology in the sintering molding process using quartz sand expansion material as a free compensation to solve the sintering process of the metal shell and PTFE lining of the difference between the coefficient of linear expansion, thermal expansion and contraction inconsistencies caused by the PTFE lining and the metal shell delamination detachment problem. PTFE lining isobaric molding technology can be applied to the geometry, structure of complex valves (ball valves, gate valves) cavity molding, to broaden and improve the temperature range of similar products and corrosion resistance, abrasion resistance, sealing reliability, widely used in petroleum, chemical industry, pesticides, dyestuffs, pharmaceuticals, military and other corrosive and serious occasions and piping system media or material transportation.
Representative products
PTFE lined general equipment is now an important industrial storage containers, giving full play to the high strength and high hardness characteristics of steel and PTFE physical and chemical properties of the perfect combination of the advantages of the majority of the tanks to solve the difficult problem of corrosion problems, and has become the mainstay of the modern anticorrosion containers.
PTFE lining equipment through certain processing technology improvement, can be realized in the higher pressure ≤ 2.5MPa use. PTFE lined equipment has been more and more widely used in chemical production enterprises with high corrosion resistance requirements.
In order to apply pressure, temperature and other complex conditions of the environment, PTFE lining structure is usually targeted to be improved, such as: adding metal mesh in the PTFE layer can reduce the thermal expansion and contraction of the PTFE lining to improve the ability to withstand negative pressure; adding polyperfluoroethylene propylene in the tetrafluoroethylene layer, to improve the resistance to deformation of the temperature resistance, and so on.
PTFE lining can be divided into two kinds: loose lining and tight lining. Loose lining is generally wrapped around the PTFE belt in the corresponding mold, sintered on the mold molding, demolded into the equipment, flanging is completed; characterized by the existence of a gap between the equipment steel body and the lining PTFE plate; applicable to the temperature change is not large and positive pressure of the transport pipeline, reaction cylinder, etc.; the advantages of the process is simple, less investment, molding fast;
Polytetrafluoroethylene lining process
Polytetrafluoroethylene PTFE is known as “King of Plastics” and has high chemical stability. The lining equipment processed with it can resist the corrosion of almost all strong acids, strong oxidizing agents, reducing agents and various organic solvents, and is also suitable for a wide range of temperatures. Through certain processing technology improvement, it can be realized in the use of higher pressure ≤ 2.5MPa. PTFE lining equipment has been more and more widely used in chemical production enterprises with high corrosion resistance requirements.
Tight lining is the surface of the treated PTFE plate, the use of special adhesives, bonded to the equipment steel body wall; characterized by the equipment steel body and lining PTFE plate tightly bonded, there is no gap; applicable to frequent changes in temperature and pressure and changes in the environment of the magnitude of the larger; the advantages are:
1. There will be no leakage point in the electric spark detection;
2. It can be lined to the whole equipment with large volume and reduce the sealing point;
3. not subject to the limitations of the shape of the equipment, can be lined with a variety of forms of equipment, such as square. The disadvantage is that the surface treatment of the steel body wall of the equipment and the quality of the binder determines the stability of the lining layer.
Due to the inherent defects of the loose lining process, more problems have arisen after application to production. Tight lining equipment, on the other hand, due to the lining of the plate can be spliced, spliced seams through the welding to make it a whole, and thus no longer subject to the constraints of the shape of the equipment. Foreign countries as early as in the 1980s, the tight lining process to replace the loose lining.
Related Keywords
Related Keywords