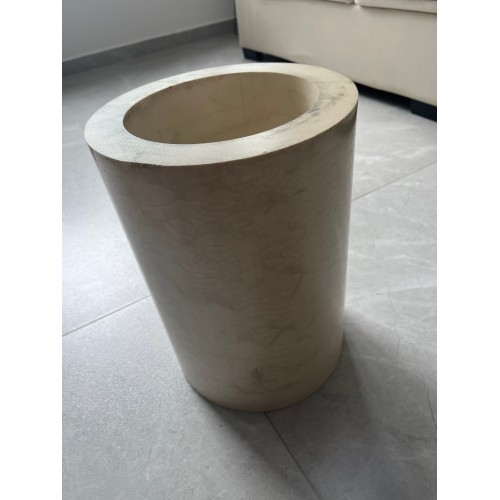
Techtron™ 1000 PPS Polyphenylene Sulfide Tube
- Min. Order:
- 1 Kilogram
- Min. Order:
- 1 Kilogram
- Transportation:
- Ocean, Land, Air, Express
- Port:
- Shenzhen, Guangzhou, Hongkong
Quantity:
Your message must be between 20 to 2000 characters
Contact NowBasic Info
Basic Info
Supply Ability: | 100 |
---|---|
Payment Type: | T/T,Paypal |
Incoterm: | FOB,CFR,CIF,EXW,DDP,DDU |
Transportation: | Ocean,Land,Air,Express |
Port: | Shenzhen,Guangzhou,Hongkong |
Product Description
Product Description
Polyphenylene sulfide (PPS) is a semi-crystalline engineering thermoplastic that bridges the gap between standard polymers and advanced polymers in terms of price and performance.PPS plastics are notable for their excellent dimensional stability and chemical resistance, making them an affordable material with advanced properties.
PPS sheets, rods and tubes have high dimensional stability during processing and use, making them ideal for complex parts with precise tolerances. In addition, PPS plastics have excellent mechanical properties, inherent electrical insulation, high heat and flame resistance.
Often used as a low-cost alternative to PEEK in applications where machining is too complex and the use of metal is too bulky, PPS plastics excel in applications that require excellent load-bearing capacity and abrasion resistance, as well as exposure to corrosive chemicals and high temperatures.
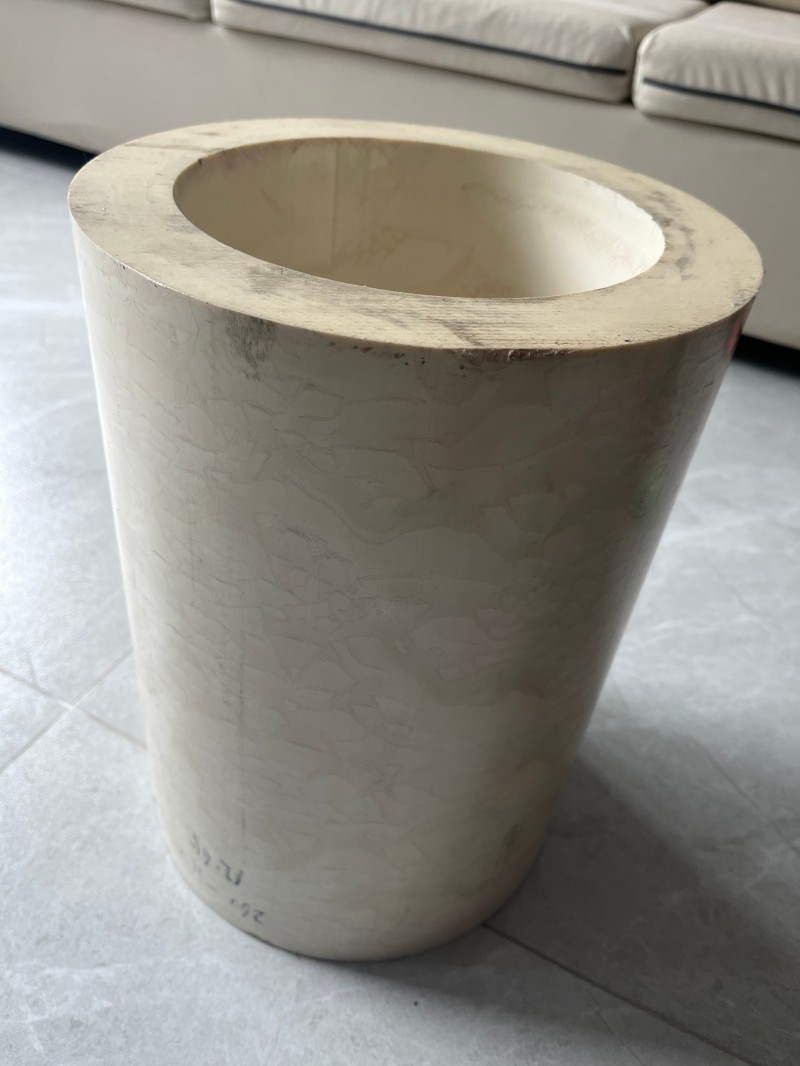
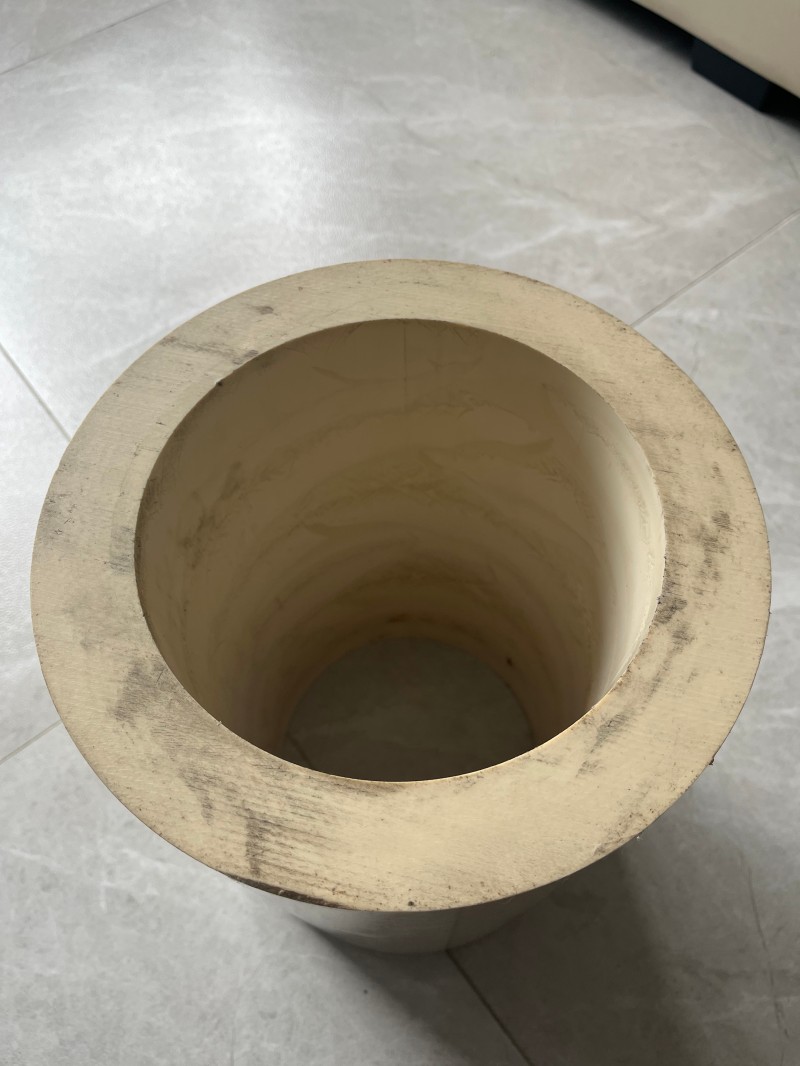
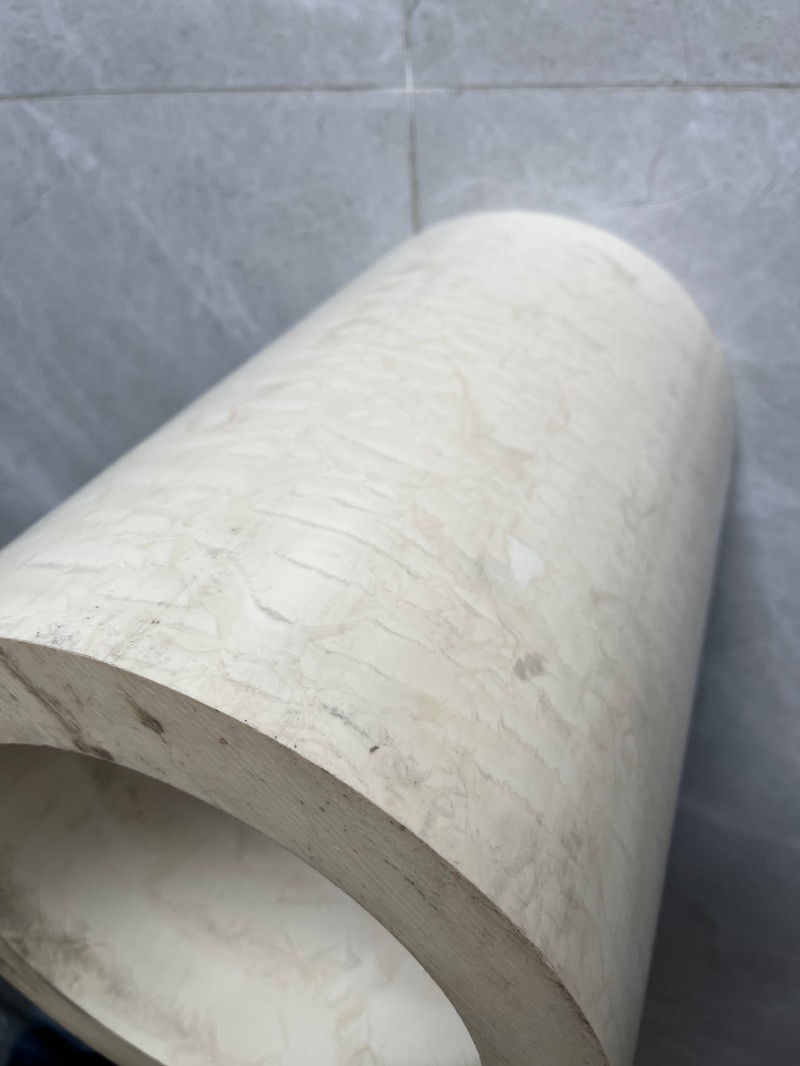
Material Properties of PPS Plastic
Thermal Properties of PPS
PPS plastics have a high degree of thermal stability and maintain many of the material's original excellent performance qualities over a wide range of temperatures.
Unless otherwise noted, the following technical specification values are based on test data for Techtron® 1000 PPS, a standard pure-grade PPS profile manufactured by the Mitsubishi Chemical Group.
Heat Distortion Temperature of PPS
The heat deflection temperature (HDT) is the temperature at which a plastic specimen begins to deform under a specific load. At a load of 1.8 MPa (264 PSI), PPS has a heat deflection temperature of 115°C (tested in accordance with ISO 75-1/2) or 250°F (tested in accordance with ASTM D648).
Maximum Allowable Use Temperature for PPS
PPS components can withstand a continuous service temperature of 220°C (425°F) (20,000 hours in air).
PPS Melting Point
PPS has a melting point of 280°C (tested in accordance with ISO 11357-1/-3) or 540°F (tested in accordance with ASTM D3418).
Thermal Conductivity of PPS
Thermal conductivity is a measure of a plastic's ability to transfer heat by conduction, and PPS plastics are more thermally conductive than PEEK, but less so than PE and PTFE.
The thermal conductivity values for PPS at 23°C/73°F are as follows:
ISO - 0.3 W/(K.m)
ASTM - 2 BTU in./(hr.ft². °F)
Flammability and Fire Resistance of PPS
PPS plastics are inherently flame retardant to UL 94 V-0 without the need for any other fillers or additives. Pure grade PPS has an oxygen index of 44% when tested in accordance with ISO 4589-1/2.
Linear Coefficient of Thermal Expansion of PPS
The coefficient of linear thermal expansion (CLTE) is used to determine the rate of expansion of a material as a function of temperature.
Overall, PPS has a lower CLTE than other engineering plastics in the same price range, such as PET and POM. This property makes PPS an excellent low-cost alternative to higher-priced materials such as PEEK and PAI in applications that require very high dimensional stability at medium to high temperatures.
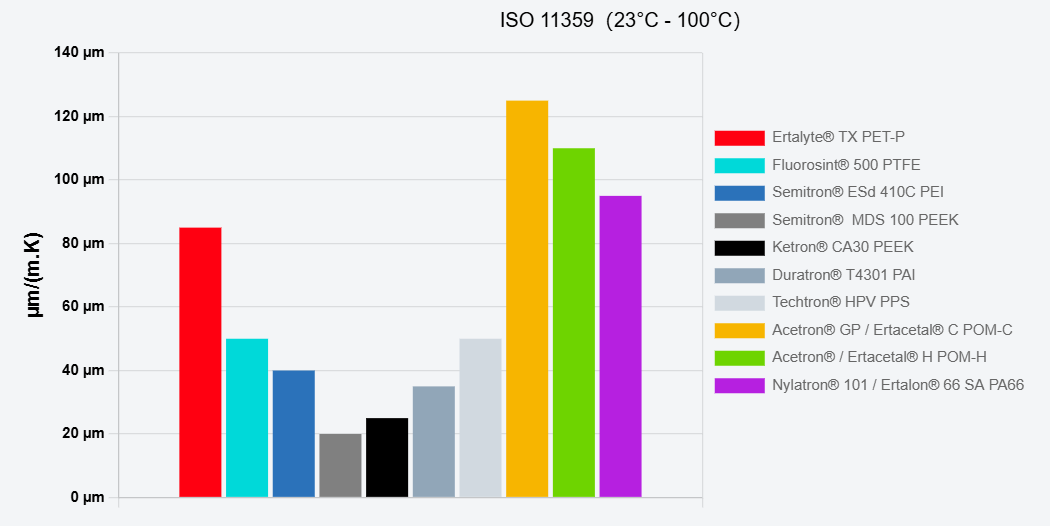
Creep resistance of PPS
Creep characterization tests are used to predict the rate of deformation of a material when subjected to a constant mechanical stress over a specific temperature range.
As shown in the graph below, after several hours of exposure to high temperatures, more stress is required to deform Techtron® HPV PPS than other common engineering plastics.The creep resistance of PPS is second only to that of PAI and PEEK materials, which are typically much more expensive than PPS.
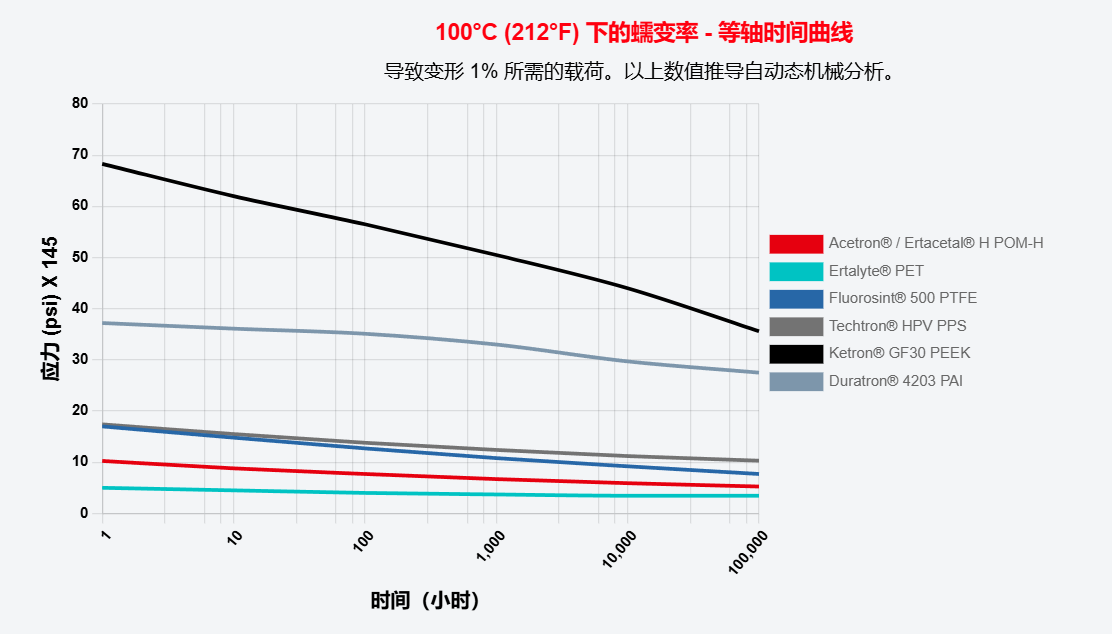
With high dimensional stability and excellent mechanical strength, PPS plastics have the ideal mechanical properties for load-bearing applications as well as for deep machining complex parts.
Unless otherwise noted, the following technical specification values are based on test data for Techtron® 1000 PPS, a standard pure grade PPS profile manufactured by the Mitsubishi Chemical Group.
Density of PPS
The density of pure grade PPS is approximately 1.35 g/cm³. Reinforced grades of PPS typically have higher densities, reaching 1.66 g/cm³ with 40% glass fiber reinforcement.
Tensile Strength of PPS
The tensile strength of PPS plastic is higher than that of other engineering plastics in the same price range. This means that the plastic can be subjected to very high stresses before fracture occurs. tensile strength, strain and elasticity values for Techtron® 1000 PPS are shown below (tested in accordance with ISO 527-1/-2 and ASTM D638):
Tensile Strength Tests for PPS
iso 427-1/-2 astm d638
Tensile Strength 102 MPa 13,500 PSI
Tensile Strain at Yield 12% 3.6
Tensile Strain at Rupture 12% 20
Tensile Modulus of Elasticity 4,000 MPa 500 KSI
Compressive Strength of PPS
PPS profiles have a tensile strength of approximately 21,500 PSI (tested in accordance with ASTM D695).
PPS Hardness and Impact Strength
PPS plastics have good hardness and impact resistance.
Rockwell Hardness, M Scale (ISO 2039-2): 100
Rockwell Hardness, M Scale (ASTM D785): 95
Rockwell hardness, R scale (ASTM 2240): 125
Charpy Impact (uncut, ISO 179-1/1eU) - no fracture
Charpy impact (notched, ISO 179-1/1eA) - 2.0 kJ/m²
Cantilever beam impact (notched, ASTM D256) - 0.60 ft.lb./in
Flexural Modulus and Flexural Strength of PPS
PPS plastic has a high flexural modulus and high flexural strength for structural applications where stiffness and load carrying capacity are critical.
PPS Flexural Tests
ISO 178 ASTM D790
Flexural Strength 155 MPa 21,000 PSI
Flexural Modulus of Elasticity - 575 KSI
Electrical Properties of PPS
PPS plastics are particularly well suited for applications requiring electrical insulation properties.PPS has a non-polar, semi-crystalline molecular structure that inhibits the movement of electrons. This makes PPS plastic a highly resistive material with poor electrical conductivity.
Unless otherwise noted, the following electrical property values for PPS are based on test data from Techtron® 1000 PPS, a standard pure grade PPS profile manufactured by Mitsubishi Chemical Corporation.
Electrical/Dielectric Strength of PPS
Electrical strength, also known as dielectric strength, is a measure of a material's ability to withstand electrical stress without electrical breakdown. This property is a key factor in determining a material's level of electrical insulation.
Pure grade PPS has a dielectric strength of approximately 18 KV/mm (tested per IEC 60243-1) or 540 V/mil (tested per ASTM D149).
Resistivity of PPS
Resistivity describes the ability of a material to prevent the flow of electrical current on its surface and within it, and PPS plastics have a higher resistivity than other common engineering plastics, making them particularly suitable for applications that require reliable insulating properties.
Pure grade PPS plastics have a surface resistivity of 10E12 Ohm/sq. (tested in accordance with ANSI/ESD STM 11.11) and a volume resistivity of 10E13 Ohm/cm (tested in accordance with IEC 62631-2-1).
Chemical Compatibility of PPS
Due to its low water absorption, PPS plastic has one of the most robust chemical compatibility of any engineering material, especially in its price range.PPS is ideal for a variety of applications where the following types of chemicals are present:
Strong acids and bases - e.g. sulfuric acid, hydrochloric acid, sodium hydroxide, potassium hydroxide
Organic solvents - e.g. alcohols, ketones, lipids and aromatic hydrocarbons
Oxidizing agents - e.g. hydrogen peroxide, chlorine
Hydrocarbons - e.g. fuels, oils and lubricants
Halogens - e.g. in situ disinfection/in situ cleaning, sanitizers, bleach
Moisture and humidity
Related Keywords
Related Keywords