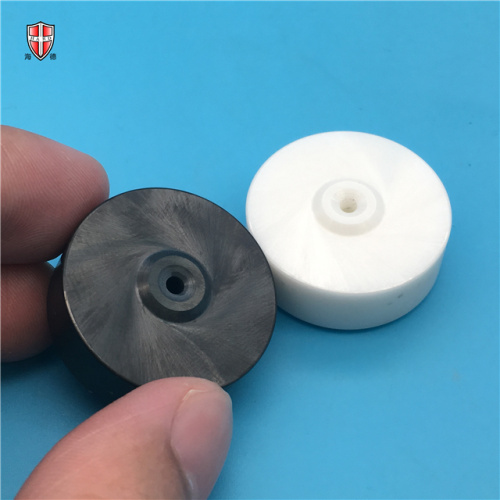
white black isostatic ZrO2 zirconia ceramic wheel roller
- Payment Type:
- L/C, T/T, D/P, Paypal, Money Gram, Western Union
- Incoterm:
- FOB
- Min. Order:
- 1 Piece/Pieces
- Min. Order:
- 1 Piece/Pieces
- Delivery Time:
- 15 Days
- Transportation:
- Ocean, Land, Air
- Port:
- Shenzhen
Your message must be between 20 to 2000 characters
Contact NowPlace of Origin: | Guangdong,China |
---|---|
Supply Ability: | 1,000,000 pcs/Month |
Payment Type: | L/C,T/T,D/P,Paypal,Money Gram,Western Union |
Incoterm: | FOB |
Certificate: | SGS |
Transportation: | Ocean,Land,Air |
Port: | Shenzhen |
white black isostatic ZrO2 zirconia ceramic wheel roller
Reputation depends on quality, quality comes from Hard!
Zirocnia Ceramics:
The most common production method of zirconia ceramics is through slurry or gas phase processing, and a few are produced by solution phase processing. All these processes are exothermic reactions involving ethylene monomer, a-olefin monomer, catalyst system (may be more than one compound) and various types of hydrocarbon diluents. Hydrogen and some catalysts are used to control molecular weight. The slurry reactor is generally a stirred tank or a more commonly used large loop reactor in which the slurry can be stirred in circulation. When ethylene and comonomer (as needed) come into contact with the catalyst, polyethylene particles are formed. After removing the diluent, the polyethylene granules or powder granules are dried and the additives are added according to the dosage to produce pellets. A modern production line with large reactors with twin screw extruders can produce more than 40,000 pounds of PE per hour. The development of new catalysts contributes to improving the performance of new grades of HDPE. The two most commonly used types of catalysts are Philips' chromium oxide-based catalysts and titanium compound-alkyl aluminum catalysts. The HDPE produced by the Phillips catalyst has a medium-width molecular weight distribution; the titanium-alkyl aluminum catalyst has a narrow molecular weight distribution. The catalyst used in the production of narrow MDW polymers in a dual reactor can also be used to produce wide MDW grades. For example, two reactors in series that produce products with significantly different molecular weights can produce bimodal molecular weight polymers that have a wide range of molecular weight distributions. Higher molecular weight results in higher polymer viscosity, but viscosity is also related to the temperature and shear rate used in the test. Rheology or molecular weight measurement is used to characterize the molecular weight of the material. HDPE grades generally have a molecular weight range of 40 000 to 300 000, and the weight average molecular weight roughly corresponds to the melt index range, that is, from 100 to 0.029g/10min (230°C, 2.16kg). Generally, higher Mw (lower melt index MI) enhances melt strength, better toughness, and ESCR, but higher Mw makes the process more difficult or requires higher pressure or temperature.
Molecular weight distribution (MWD): The WD of PE varies from narrow to wide depending on the catalyst used and the processing process. The most commonly used MWD measurement index is the unevenness index (HI), which is equal to the weight average molecular weight (Mw) divided by the number average molecular weight (Mn). This index range for all HDPE grades is 4-30. The narrow MWD provides low warpage and high impact during the molding process. The medium to wide MWD provides processability for most extrusion processes. Wide MWD can also improve melt strength and creep resistance.
Data Sheet↓
Color: CustomizedDensity: 6.0g/cm3
Zirconia Content: 94.4%
Gas permeability: 0
Water Absorption: 0
Crystal Size: 0.5um
Rockwell Hardness(45N): 78R45N
Vickers Hardness (Load 500g): 11.5(1175)Gpa(Kg/mm²)
Flexural Strength(20°C): 800Mpa
Compressive Strength(20°C): 2000Mpa
Modulus of Elasticity(20°C): >200Gpa
Thermal Conductivity(20°C-400°C): 2.5W(m.K)
Thermal Expansion Coefficient: 9.6 10-6/°C
Thermal Shock Resistance: 250 △T°C
Application industry:
Machinery, fiber optic, knife, medical, food, petroleum etc.
Specific application:
plunger, ceramic shaft, fiber optic bushing, stub, grinding, ceramic knife, ceramic slide guide, machined plunger, mobile phone shell, watch case, haircut razor blade etc.
1.12 years of professional production industrial ceramics factory
2.High quality products with low price
3.High precision parts with lowest tolerance
4.Short time for production
5.Has a group of experienced, professional and efficient R&D team
6.Has a good reputation in China and abroad.
7.MOQ is not limited, small quantity is welcome.
8.Vigorous team and good after-sales service
FAQ
Q: Are you trading company or manufacturer ?
A: We are factory.
Q: How long is your delivery time?
A: Generally it is 5-10 days if the goods are in stock. or it is 15-30 days if the goods are not in stock, it is according to quantity.
Q: Do you provide samples ? is it free or extra ?
A: Yes, we could offer the sample for free charge but do not pay the cost of freight.
Q: What is your terms of payment ?
A: Payment<=1000USD, 100% in advance. Payment>=1000USD, 50% T/T in advance ,balance before shippment.
Related Keywords