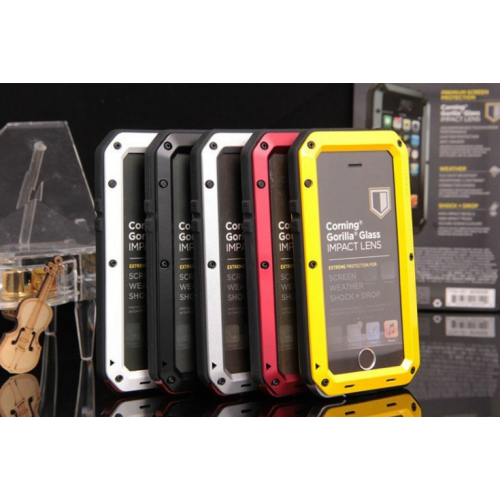
Special oxidation of the shell
- Payment Type:
- T/T
- Min. Order:
- 10 Bag/Bags
- Min. Order:
- 10 Bag/Bags
- Delivery Time:
- 7 Days
- Transportation:
- Ocean, Land, Air
- Port:
- SHENZHEN, Guangzhou, Shanghai
Quantity:
Your message must be between 20 to 2000 characters
Contact NowBasic Info
Basic Info
Place of Origin: | China |
---|---|
Productivity: | China |
Supply Ability: | good |
Payment Type: | T/T |
Transportation: | Ocean,Land,Air |
Port: | SHENZHEN,Guangzhou,Shanghai |
Product Description
Product Description
Anodic oxidation can significantly improve the corrosion resistance of aluminum alloy, improve the surface hardness and wear resistance of aluminum alloy, and have good decorative performance after proper coloring [1]. There are three kinds of anodizing technology for aluminum and its alloy anodizing film: chemical staining, electrolytic coloring and electrolysis whole color [2]. Chemical staining is the use of porous and chemical properties of the oxide film
Pingshan auto parts secondary anode oxidation factory, professional surface treatment
The color of the oxidation film is made by the adsorption of various pigments, according to the coloring mechanism and process, which can be divided into organic dyes, inorganic dyes, color printing, color dyeing, and colorless dyeing. Electrolytic coloring is after anodic oxidation of aluminum and its alloys in aqueous solution containing metal salt electrolytic communication, at the bottom of the porous oxide film layer deposited metal, metal oxide or metal compounds, due to the effect of scattering of the light electricity deposits and presents a variety of color. Electrolytic refers to overall shaded in anodic oxidation of aluminum and its alloy at the same time being shaded, its characteristic is one step oxidation and shaded, coloring film with good light resistance, heat resistance, corrosion resistance and wear resistance
Al2O3 film is formed on the surface of aluminum and its alloys by ordinary anodic oxidation, and the Al2O3 membrane structure is different with different anodic oxidation. When anodizing, the growth of the oxide film on the aluminum surface consists of two processes: electrochemical generation and chemical dissolution of the membrane. The film can only grow and thicken when the film grows faster than the dissolution rate. 1, aluminum alloy after anodic oxidation, surface pores, special aluminum oxide dyes, according to certain concentration of dissolved with water, put a good aluminum oxide in the dye solution, dye molecules can adsorption in porous aluminum oxide film, this is aluminum oxidation coloring. 2, color can be rich and colorful, any color can be dyed after 3, aluminum oxidation dyeing, also need to seal the hole, is the micro porous seal, this oxidation of the dye molecules in the micropore membrane will not loss, increasing the function and adornment effect on the surface of the aluminum shenzhen or chi hing oxide metal products co., LTD is mainly engaged in aluminum alloy surface oxidation treatment (anode) has more than ten years experience in management technology. Our company is seeking "high quality, high grade, high efficiency" as the development model to "respect the individual serving customers and strive for excellence". Anodizing of aluminum alloy: electrochemical oxidation of metal or alloy. A metal or alloy plate is used as an anode, and an electrolytic method is used to form oxide films on its surface. The metal oxide film changes the surface state and properties, such as surface shading, improving corrosion resistance, enhancing wear resistance and hardness, protecting metal surface and so on. For example, anodic oxidation of aluminum, aluminum and its alloys are placed in the corresponding electrolyte (such as sulfuric acid, chromic acid, oxalic acid, etc.) as the anode and electrolysis under certain conditions and external current. Anodic aluminum or its alloy oxidation, the surface of alumina thin layer, its thickness is 5 ~ 20 microns, hard anodic oxide film can reach 60 ~ 200 microns. After anodic oxidation of aluminum or its alloy and improve its hardness and wear resistance, can reach 250 ~ 500 kg per square millimeter, good heat resistance, hard anodic oxidation film melting point as high as 2320 k, excellent insulation, resistance to breakdown voltage of 2000 v, to enhance the corrosion resistance, hitches in omega = 0.03 NaCl salt fog corrosion thousands of hours. The thin layer of oxide film has a large number of micropores, which can absorb various kinds of lubricants, suitable for making engine cylinder or other wear-resisting parts. The film microporous adsorption ability can be colored into various beautiful and colorful colors. Non-ferrous metal or its alloy (such as aluminum, magnesium and its alloys, etc.) can be anodic oxidation treatment, this method is widely used in mechanical parts, aircraft parts, precision instruments and radio equipment, household goods and building decoration, etc.
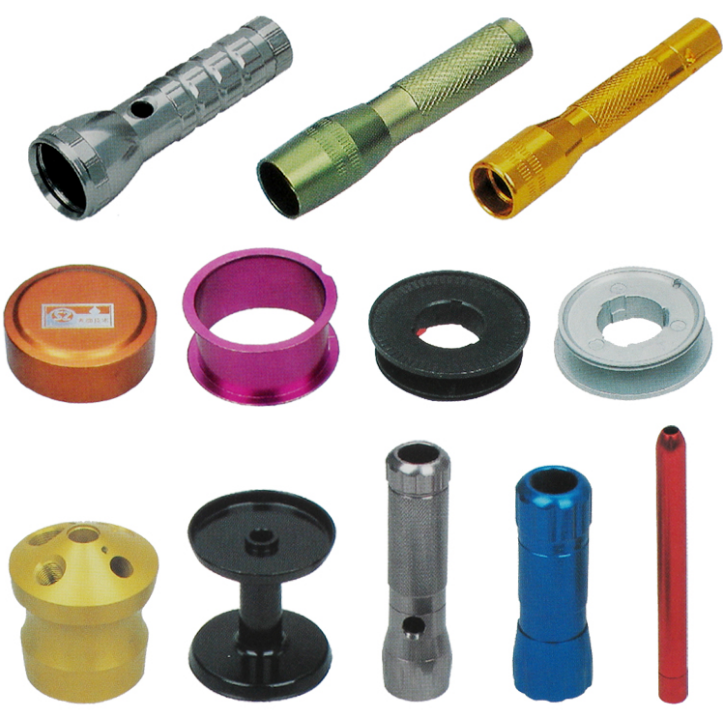
Pingshan auto parts secondary anode oxidation factory, professional surface treatment
The color of the oxidation film is made by the adsorption of various pigments, according to the coloring mechanism and process, which can be divided into organic dyes, inorganic dyes, color printing, color dyeing, and colorless dyeing. Electrolytic coloring is after anodic oxidation of aluminum and its alloys in aqueous solution containing metal salt electrolytic communication, at the bottom of the porous oxide film layer deposited metal, metal oxide or metal compounds, due to the effect of scattering of the light electricity deposits and presents a variety of color. Electrolytic refers to overall shaded in anodic oxidation of aluminum and its alloy at the same time being shaded, its characteristic is one step oxidation and shaded, coloring film with good light resistance, heat resistance, corrosion resistance and wear resistance
Al2O3 film is formed on the surface of aluminum and its alloys by ordinary anodic oxidation, and the Al2O3 membrane structure is different with different anodic oxidation. When anodizing, the growth of the oxide film on the aluminum surface consists of two processes: electrochemical generation and chemical dissolution of the membrane. The film can only grow and thicken when the film grows faster than the dissolution rate. 1, aluminum alloy after anodic oxidation, surface pores, special aluminum oxide dyes, according to certain concentration of dissolved with water, put a good aluminum oxide in the dye solution, dye molecules can adsorption in porous aluminum oxide film, this is aluminum oxidation coloring. 2, color can be rich and colorful, any color can be dyed after 3, aluminum oxidation dyeing, also need to seal the hole, is the micro porous seal, this oxidation of the dye molecules in the micropore membrane will not loss, increasing the function and adornment effect on the surface of the aluminum shenzhen or chi hing oxide metal products co., LTD is mainly engaged in aluminum alloy surface oxidation treatment (anode) has more than ten years experience in management technology. Our company is seeking "high quality, high grade, high efficiency" as the development model to "respect the individual serving customers and strive for excellence". Anodizing of aluminum alloy: electrochemical oxidation of metal or alloy. A metal or alloy plate is used as an anode, and an electrolytic method is used to form oxide films on its surface. The metal oxide film changes the surface state and properties, such as surface shading, improving corrosion resistance, enhancing wear resistance and hardness, protecting metal surface and so on. For example, anodic oxidation of aluminum, aluminum and its alloys are placed in the corresponding electrolyte (such as sulfuric acid, chromic acid, oxalic acid, etc.) as the anode and electrolysis under certain conditions and external current. Anodic aluminum or its alloy oxidation, the surface of alumina thin layer, its thickness is 5 ~ 20 microns, hard anodic oxide film can reach 60 ~ 200 microns. After anodic oxidation of aluminum or its alloy and improve its hardness and wear resistance, can reach 250 ~ 500 kg per square millimeter, good heat resistance, hard anodic oxidation film melting point as high as 2320 k, excellent insulation, resistance to breakdown voltage of 2000 v, to enhance the corrosion resistance, hitches in omega = 0.03 NaCl salt fog corrosion thousands of hours. The thin layer of oxide film has a large number of micropores, which can absorb various kinds of lubricants, suitable for making engine cylinder or other wear-resisting parts. The film microporous adsorption ability can be colored into various beautiful and colorful colors. Non-ferrous metal or its alloy (such as aluminum, magnesium and its alloys, etc.) can be anodic oxidation treatment, this method is widely used in mechanical parts, aircraft parts, precision instruments and radio equipment, household goods and building decoration, etc.
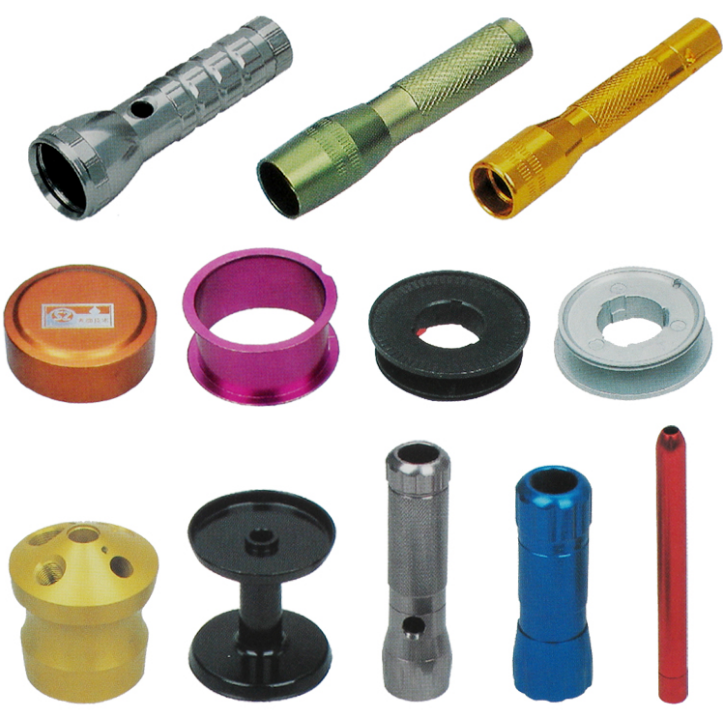
Related Keywords
Related Keywords