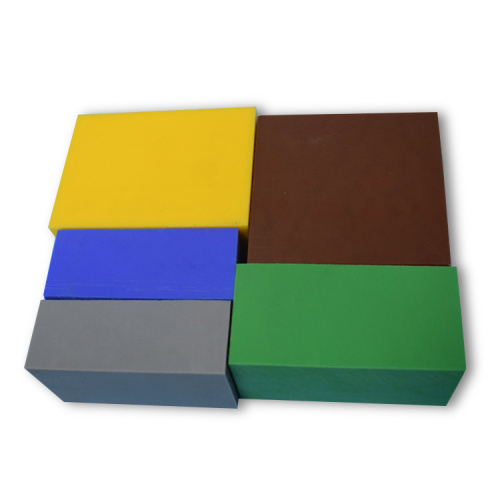
Advanced POM Special-Shaped Parts for Precision Industries
- Min. Order:
- 1 Others
- Min. Order:
- 1 Others
- Transportation:
- Ocean, Land, Air
- Port:
- SHEKOU
Your message must be between 20 to 2000 characters
Contact NowPlace of Origin: | shenzhen |
---|---|
Productivity: | >5000kg |
Supply Ability: | >10000kg |
Certificate: | Roth and SGS |
HS Code: | 3920999090 |
Transportation: | Ocean,Land,Air |
Port: | SHEKOU |
Introduction
POM-C (Polyoxymethylene Copolymer) sheets are widely recognized for their high rigidity, low friction, and dimensional stability. However, machining large components (over 1m in length) often leads to warping due to internal stress accumulation. This article explores an innovative approach combining high-precision milling, meticulous grinding, and secondary tempering to produce distortion-free POM-C parts, addressing a critical challenge in aerospace, automotive, and industrial automation sectors.
Why Does POM-C Warp During Machining?
POM-C’s semi-crystalline structure makes it prone to deformation under mechanical and thermal stress:
-
Residual Stress from Milling:
-
Cutting forces and tool friction generate localized heat (up to 80–100°C), disrupting the crystalline regions and creating uneven internal stresses.
-
Longer machining paths (>1m) exacerbate stress gradients, causing curvature or twisting.
-
-
Material Anisotropy:
-
Extruded POM-C sheets have directional molecular alignment. Unbalanced machining can trigger asymmetric stress release.
-
-
Hygroscopic Expansion:
-
POM-C absorbs moisture post-machining, leading to swelling and dimensional shifts (up to 0.5% in humid environments).
-
Advanced Machining Protocols to Combat Warpage
1. High-Precision CNC Milling with Stress Mitigation
-
Machine Requirements:
-
Rigid Frame CNC Mills: Minimize vibration (e.g., 5-axis machines with ≤5μm positional accuracy).
-
Coolant Strategy: Oil-based coolants maintain temperatures below 60°C to suppress thermal stress.
-
-
Toolpath Optimization:
-
Climb Milling: Reduces tool engagement force by 20% compared to conventional milling.
-
Multi-Pass Roughing: Removes material in layers (0.5mm/pass), preventing concentrated heat buildup.
-
Related Keywords